High-Performing Hydrodynamic Bearings
Hydrodynamic bearings are widely used in high-performance machinery to provide reliable operation over extended periods of time. Hydrodynamic bearing operation is largely non-contacting, providing theoretically infinite life when properly designed and maintained.
These bearings play a critical role in the operation of equipment found in power generation plants, oil refineries, petrochemical plants and other process plants, and in large marine propulsion machinery.
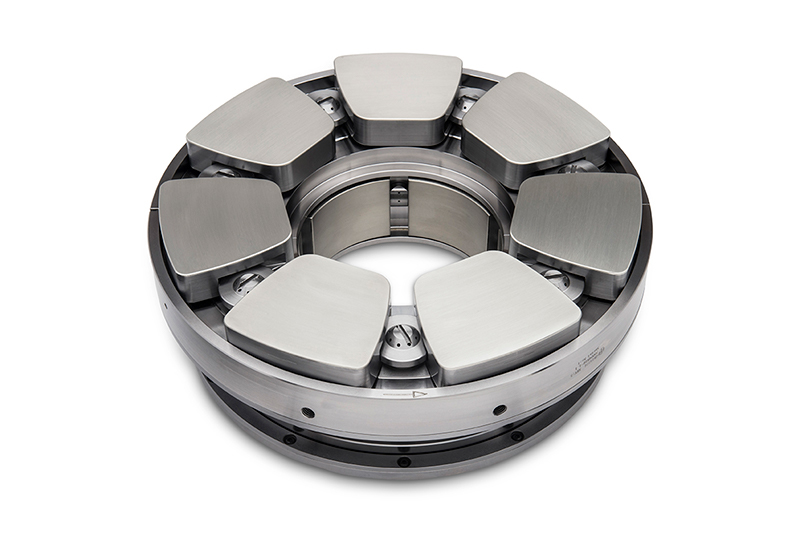
Hydrodynamic Bearing Requirements
Hydrodynamic bearings require three elements to generate the hydrodynamic film:
Viscous fluid (the lubricant)
Relative motion (the sliding action of one surface relative to another)
Converging geometry
In journal bearings, the converging geometry is provided by the slight difference in diameters of the shaft and the bore of the bearing. For improved static and dynamic performance, a defined profile can be machined into the bearing. Tilt pads are often used if stability is an issue, if varying conditions must be accommodated or if other bearing performance parameters require optimization.
In thrust bearings, the converging geometry is either machined into the face of a fixed plate or provided by the tilting action of tilt pad thrust bearings. A fixed geometry is designed for a specific condition, while tilt pad bearings are often used to accommodate changing conditions.
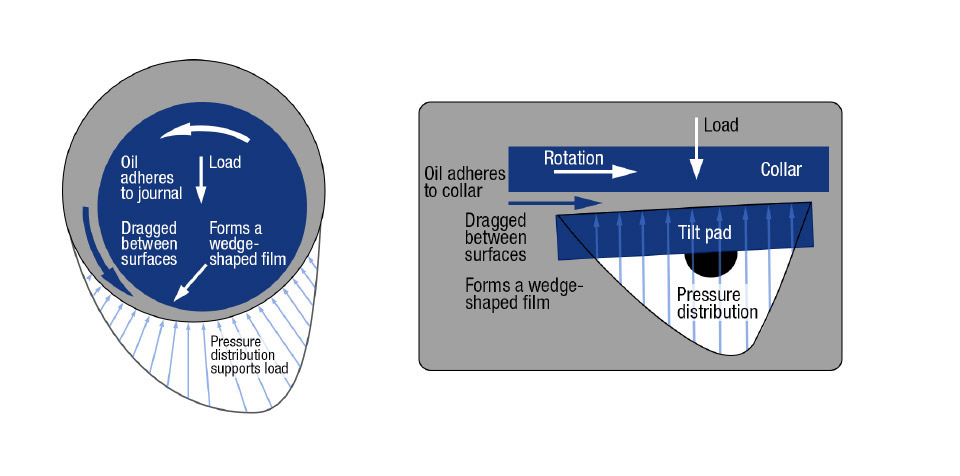

Hydrodynamic or Fluid Film?
While “hydrodynamic” and “fluid film” are often used synonymously, fluid film bearings also include hydrostatic bearings.
Hydrostatic bearings use an external source to supply the necessary film pressure between surfaces. Hydrodynamic bearings generate the pressure through the relative motion of the surfaces and the converging geometry.
Waukesha Bearings specializes in hydrodynamic fluid film bearings, but may also incorporate features of hydrostatic bearings. A primary advantage of hydrostatic bearings is the ability to generate a separating oil film without relative motion of the bearing surfaces. A hydrostatic lift feature incorporated into a hydrodynamic bearing design provides a separating film prior to shaft rotation. This prevents contact of surfaces at start-up and the potential damage which might occur to the surfaces of heavily loaded bearings as they go through the boundary and mixed film regimes.

Performance Optimization
Waukesha Bearings supplies medium and thick wall journal bearings specifically designed for turbomachinery. Several configurations are available to handle application needs for load capacity, rotating load, stiffness, damping, and rotordynamic stability.
The addition of grooves to fixed profile bearings can reduce destabilizing effects due to fluid rotation, while alterations to the circular geometry provide additional stability gains.
Performance can also be optimized through bearing material and lubrication method. Lubrication may be pressure fed or self-lubrication, the latter typically with an oil ring. Polymer linings can be used to extend performance limits or withstand high ambient temperatures. Hydrostatic jacking is recommended for machines with high start-up loads.
Sleeve Bearing Geometries
Plain Sleeve
Plain sleeve bearings are cylindrical bearings, typically horizontally split and with the lubricant supplied through axial grooves located at the horizontal joint.

Multi-lobe
Most multi-lobe bearing designs have three or four lobes, which can be centered for bi-directional rotation or offset for uni-directional rotation. Specialized designs may also have plain segments in the loaded region and tapered segments in the remaining areas. The multi-lobe bearing provides increased stability over plain sleeve bearings. They are typically used in high-speed machinery with light rotors.
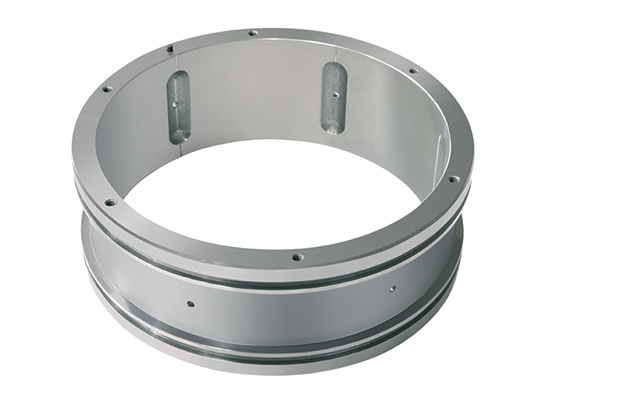
Lemon Bore
A specific kind of multi-lobe bearing, the lemon bore bearing has two large lobes offset about the center, giving them an elliptical shape. The vertical clearance is slightly smaller than the horizontal clearance. The design suppresses oil whirl with a vertical preload and can improve stiffness and damping over a plain sleeve bearing.

Pressure Dam
One of the most stable fixed geometry bearings available, the pressure dam bearing has a characteristic relief track, machined into the upper (unloaded) half, that comes to an abrupt end (pressure dam) to create an artificial load on the journal. This artificial load forces the shaft into a more eccentric position, resulting in greater stability.
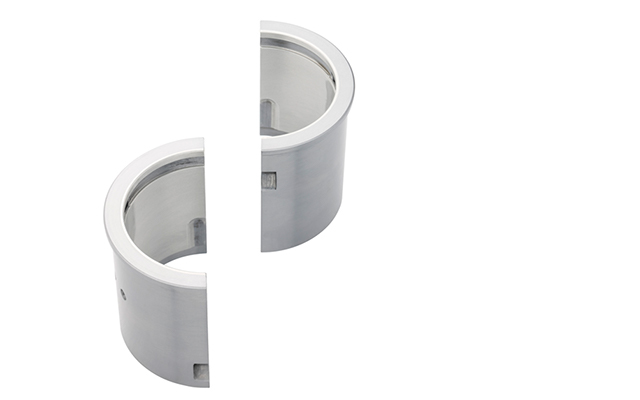
Offset Half
The upper and lower halves of an offset half bearing are displaced transverse to the shafts axis for greater stability than plain sleeve bearings.